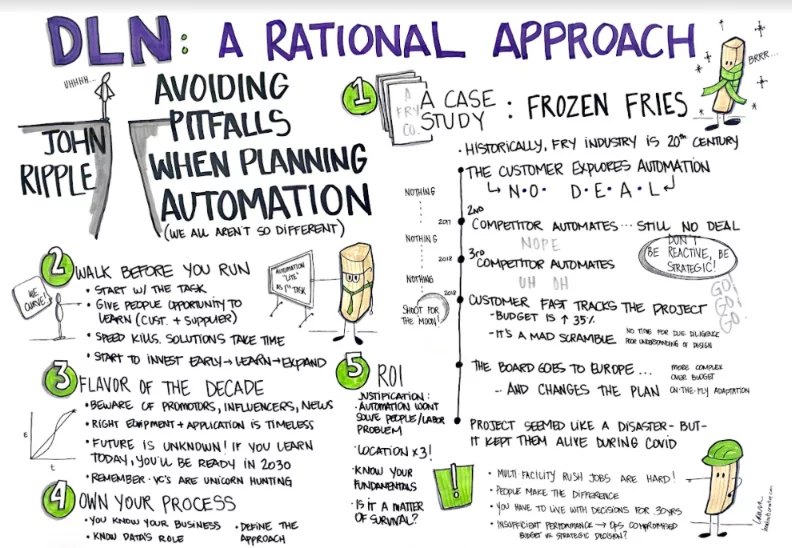
The second post in our series recapping our recent educational conference will cover the talk of John Ripple, material handling expert with hands-on experience in global markets. He consults on complete project life-cycle experience: concept & application, design development through simulation/emulation, implementation including project planning and execution, testing, start-up, go-live, and support.
John’s topic was Avoiding Pitfalls in Your Automation Project, and he used his 20 plus years of experience to share stories and suggestions based on what he’s seen in the industry.
How A Frozen Fries Company Saved 3 Plant Closures… the Hard Way
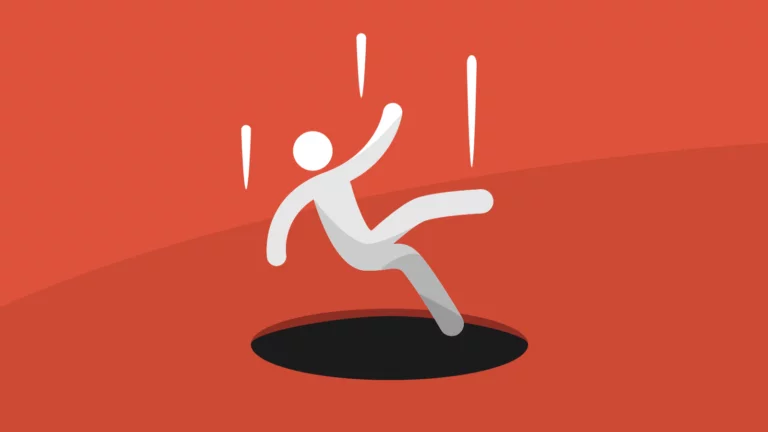
John used his background working on over a hundred large scale projects to begin with a story of what NOT to do. He told of a frozen fries company who supplied a major global fast food brand using outdated distribution centers. John and team presented a plan for a state of the art, thoughtfully designed automated system that would produce an ROI in 5 – 7 years. The decision makers decided that ROI wasn’t solid enough and tabled the plan.
The next year their competitor unveiled a modern DC and the customer asked for the plan to be dusted off for another look. It was more expensive due to rising materials costs but still had an ROI of 5 – 7 years, and they tabled it again.
The following year a second competitor build an automated, updated distribution center and the fast food chain started encouraging all suppliers play at this efficient new level.
The customer’s board panicked and started insisting they move quickly. Even with a 30% materials increase from the previous plan, the shovels started flying. The anxious customer greenlighted a total of 3 facilities at enormous cost, with a lot of design fine-tuning happening on the fly. The process was messy, painful and expensive.
The ROI remained the same at 5 – 7 years with all the materials costing more. Yet in spite of the challenges, the new facilities were so much more efficient, the project ended up preventing all 3 plants from shutting down.
Common Denominators to Avoid. And How to Be Better.
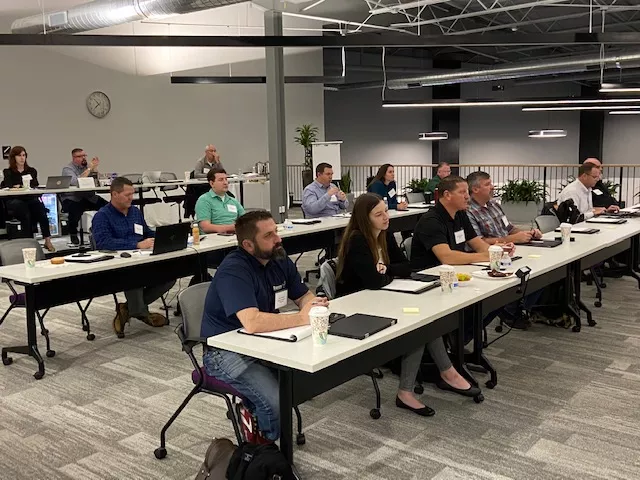
In helping get large-scale automation projects done, John often sees companies take the approach of the frozen fries company: “Get ideas. Do nothing, do nothing, do nothing, do nothing. Then Shoot for the Moon!” where companies react to competition in a hot rush to upgrade their facilities.
John has found that speed kills, whereas solutions take time. There is a definite people curve involved that is often overlooked, which leads to expectations not being reasonable.
The better way is to walk. Then run. Start with “automation lite” that focuses on tasks, not processes. Give people a chance to learn, for both the company and the suppliers.
Flavor of the Decade
When it comes to selecting the best ways to automate, John shared a run down of the “must have” equipment of the past several decades. The 80s had miniload cranes, the 90s had carousels, the 00s had cranes – and inventory was officially a bad thing, the 10s offered shuttles, and we’re seeing the 20s feature mobile robots and cubes.
He cautioned the audience to not feel pressured to buy the hottest new thing — unless it really made sense for those facilities.
Best Practices
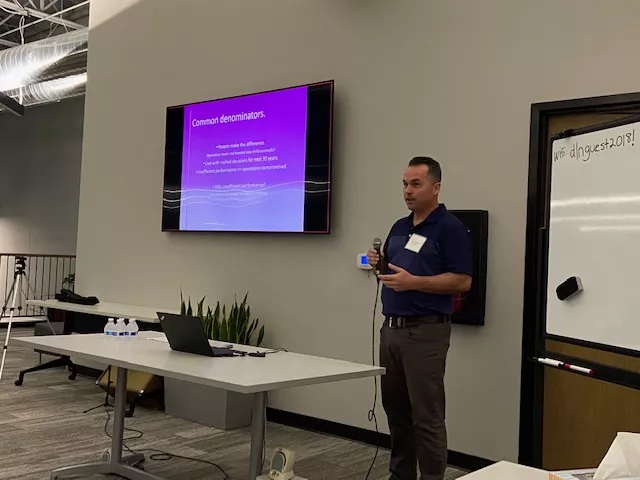
Ultimately John suggested that decision makers own the process. Under this comes defining the approach, evaluating customer needs, risk tolerance, timing and investment. If you know what leadership values, you can offer recommendations that align with those values.
When it comes to ROI and justifying automation upgrades, John points out that the labor savings alone won’t get you there. People problems are not solved by robots. Look at location, timing, profits that can be re-invested into more improvements (which is the Amazon way).
Paralysis is the worst option!
What do you think? If you need help taking baby steps to automation so you can walk – then run – with your facility improvements, we are happy to offer our advice.