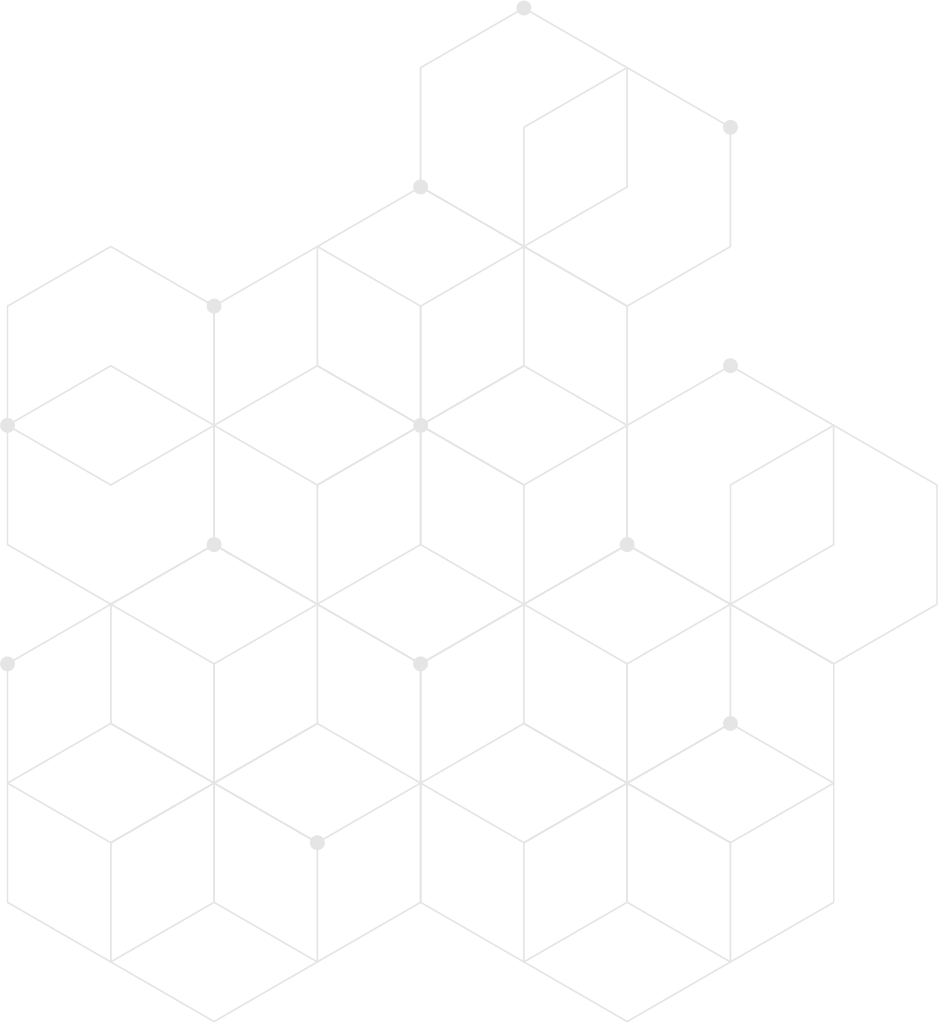
Supply Chain Consulting
Strategy
We start by analyzing your business objectives and distribution network. After assessing your current infrastructure, we model alternative scenarios to develop a strategy that lowers costs while improving service and operational performance.
Distribution Network Analysis
Using your data and requirements, we define the optimal number of network nodes and ideal geographical distribution.
Capacity Planning
We determine the optimal way to meet future requirements by expanding or modernizing existing infrastructure, building new nodes in your network, or securing outsourced capacity.
Inventory Deployment Strategy
Our comprehensive analysis of your orders, locations, product categories, velocity, seasonality, and other factors helps identify different fulfillment options for your SKU assortment.
Operational Assessment
Our team helps you identify and prioritize opportunities to enhance existing operations, which will extend your facility’s lifespan and improve its performance.
Observation Of Operation
Our skilled team will tour your operation and observe product flows, current handling processes, and existing equipment to identify quick wins and opportunities for improvement.
Equipment Audit
We’ll evaluate how outdated equipment or inefficient layouts may be slowing your throughput. We’ll also outline a value-driven plan to make strategic upgrades, including repurposing or refurbishing existing infrastructure where appropriate.
Data-based Optimization
We can uncover operational inefficiencies after insightful analysis of your order data, labor productivities, cycle times, or other operational aspects like routing, waving, or slotting.
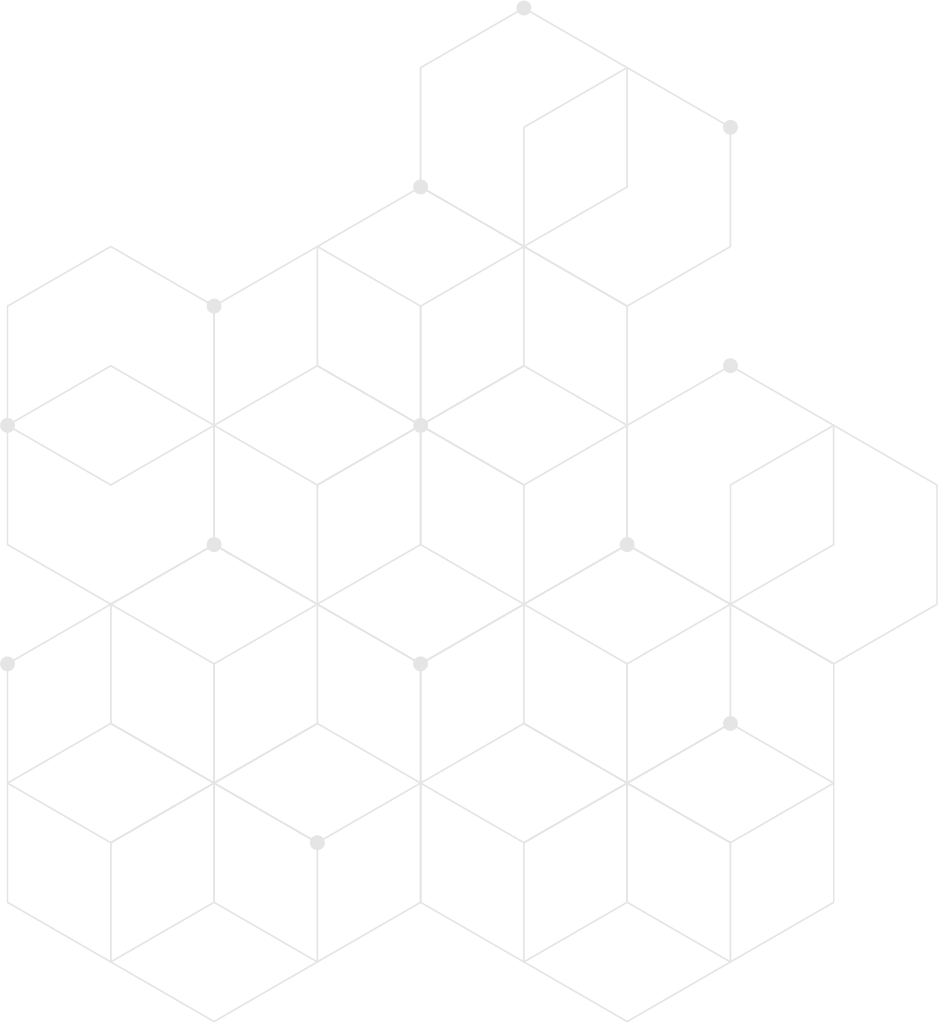
Data-driven Engineering Studies
Whether you need to augment an existing facility to meet business requirements or design an entirely new distribution center, DLN’s experienced team of consultants and engineers will partner with you to create a comprehensive plan for future operations. We value an iterative approach to ensure that our recommended solutions address your specific challenges. This results in a sound business case rooted in your data and requirements.
Data Analysis & Requirements Gathering
Before discussing design or equipment, we develop a deep understanding of your current and future needs. We begin with a detailed analysis of your data, creating insightful visualizations that inform design parameters and guide discussion on business outlook and operational requirements.
Concept Hypothesis & Facility Sizing
Based on the new design parameters and identified opportunities, we conceptualize practical and implementable concepts. Then, we agnostically evaluate options to determine the best fit for your application.
Custom Automation
DLN has in-house capabilities to develop custom automation and robotic solutions. Custom automation can be an ideal solution for manual operations that are highly repetitive, have challenging ergonomics or working conditions, or require high degrees of accuracy.
Solution Development & Business Case
Our engineering and implementation expertise is then applied to generate comprehensive material handling solutions and accurate investment estimates. We closely partner with stakeholders to create a business case that shows a sound financial justification for the recommended solution.
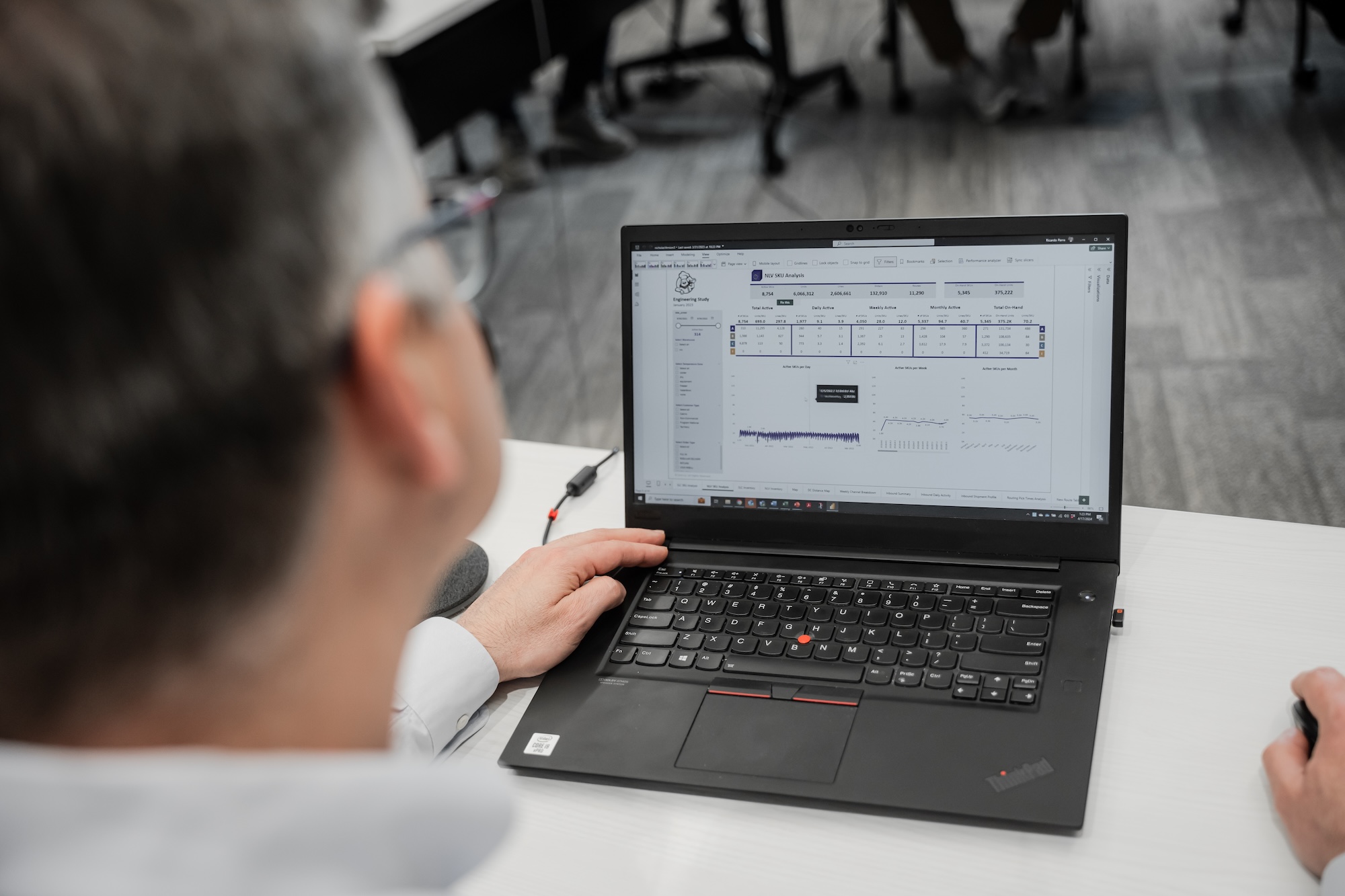
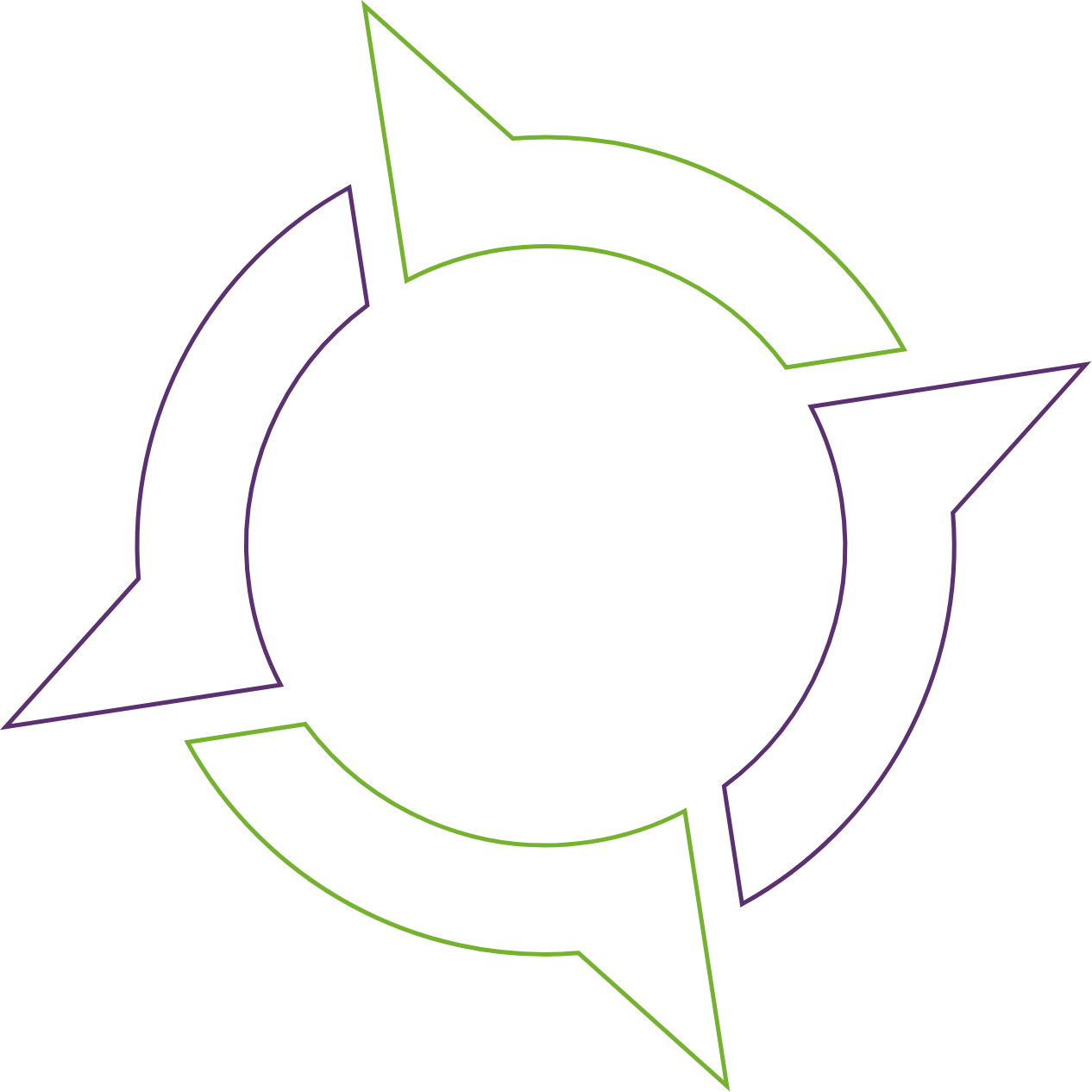