By Luke Nuber, Director of Sales Operations & Sr. Account Executive, DLN Integrated Systems, Inc.
Part one of a two-part series. Click here to read part 2: Roadmap to Warehouse Modernization Success.
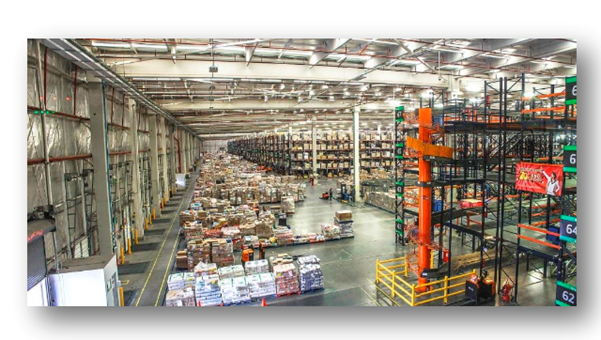
An aging, legacy distribution center brings many challenges.
These range from substandard operational performance to space constraints that limit growth opportunities. The hurdles can easily turn into competitive disadvantages.
That’s why it is crucial to consider upgrading from legacy in this highly competitive environment. Many companies face difficulties in identifying the best time to upgrade and in deciding whether to build a new facility or modernize an existing one.
Leaders should learn to recognize the signs that an upgrade is needed.
”While some companies may decide to build new, the best choice for most organizations is modernizing an existing warehouse.
Identifying When It’s Time to Upgrade
How can leaders tell if an aging DC is holding back a business? Here are some of the key indicators that it’s time for an upgrade.
- Declining Overall Performance: The current facility is no longer as agile and efficient. Processes have become more inefficient and labor-intensive.
- Market Pressures: Market changes are demanding more robust DC capabilities.
- Reduced Speed and Accuracy: The DC is challenged to keep up with new requirements for fulfilment speed and order accuracy.
- Assortment and Cost Hurdles: The facility can’t handle the growing breadth of assortment and is struggling to maintain low costs.
- Competitive Challenges: Competitors have gained advantage through more robust DCs.
Upgrading with Best Practices in Mind
With the right investments, a legacy warehouse can become robust once again. Companies can capture significant value from their existing facilities if they upgrade strategically. This requires understanding optimization best practices and having a picture in mind of what best-in-class looks like across several key performance metrics: speed, accuracy, assortment and cost.
Boosting Speed Through Improved Cycle Times
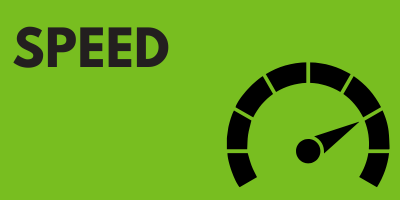
Speed is a critical competitive factor in DCs today. The key to boosting speed is measuring and improving cycle times — the length of time a repetitive process takes to complete one cycle. Common examples of cycle times include the time it takes to pack an order or the length of time between placement of an order and when it leaves the DC.
One approach to increasing speed is to use waveless warehouse execution software — which is ideal for optimizing the sequence of orders at each step of the process while also enabling select orders to be expedited immediately.
Another strategy is to boost the productivity of warehouse workers. This can be accomplished by moving away from time-intensive person-to-goods processes in which pickers walk through a warehouse to find items. Most pickers in a person-to-goods process spend over 50% of their time walking, which is a non-value-add activity. Instead, many companies are moving to goods-to-person processes in which items are brought to workers by leveraging automation, such as robotic systems, that eliminate walking from the process altogether.
Improving Accuracy with Technology
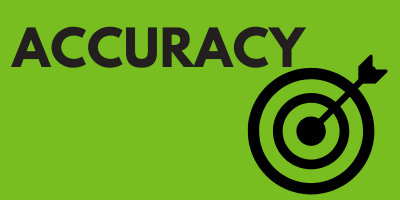
Order accuracy is crucial to any warehouse operation, and there are a number of proven technologies that boost accuracy by ensuring the correct items are picked and get into the right orders. One example is pick-to-light or put-to-light systems that provide visual indicators to pickers on which items to select and where to put them. Other systems like GTP and AMRs also include screens that display images of items to be picked, helping the operators to visually confirm that they have the correct items.
Mitigating Assortment Growth through Storage Strategies
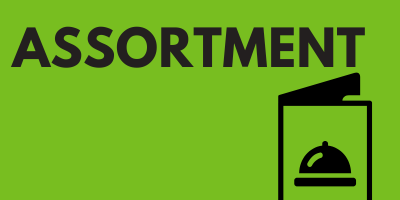
Expansion of SKU assortments within DCs challenges storage capacity and erodes productivity by making pick paths longer. This reality requires new approaches to overcome the hurdles. The ideal solution is to leverage high density, high selectivity storage, which reduces the space between items without the creation of blocking. This enables pickers to access items quickly and creates additional space to bring in more items as needed.
Keeping Costs Low with Packing Automation
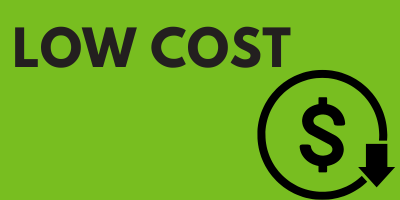
Fulfillment cost is a metric that interests all companies, whether to improve their competitive position or profitability. Picking is usually the main focus. However, an often-overlooked opportunity involves costs on the packing side. Automations such as auto baggers or auto box erectors help to boost efficiency and drive reduced labor costs. On the materials side, auto baggers and box-on-demand technology reduce the package size to exactly what is needed. This cuts material costs by reducing the packaging and the void-fill materials in boxes and drives down shipping fees by avoiding the shipping of excess air.
Building a New Facility is Prohibitive for Most Organizations
Most companies face enormous hurdles in justifying the building of new facilities, including these:
Modernizing is the Best Choice for Most Companies
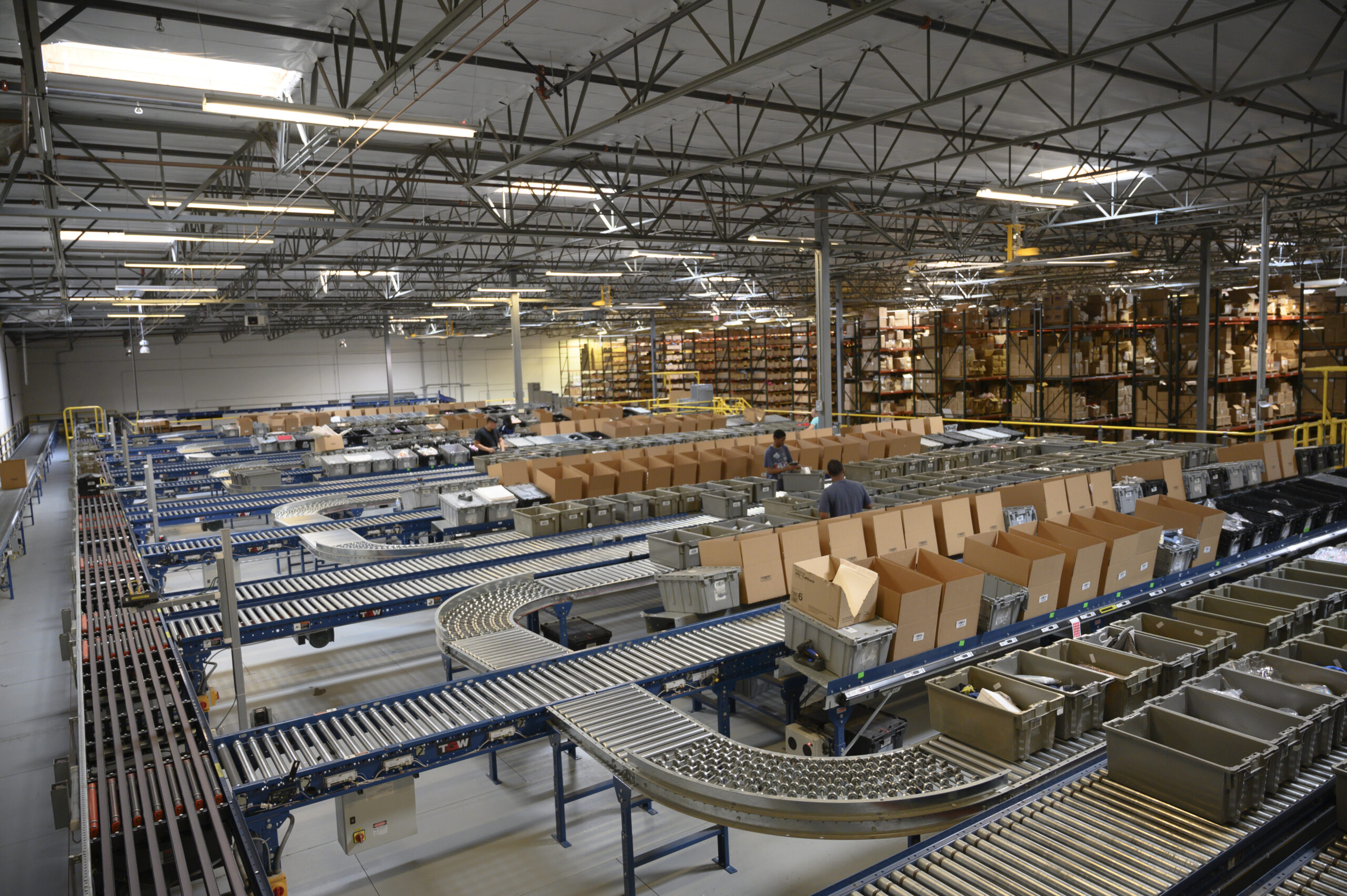
Most companies will benefit from modernizing rather than pursuing greenfield warehouse projects. Modernizing enables organizations to leverage existing assets, improve affordability, and speed the time of completion of a project.
”The key is to start with the optimization best practices in mind and examine which aspects of a warehouse are behind the times and need to be upgraded to stay competitive.
Drive Success with a Trusted Partner
Warehouse upgrade decisions vary based on the specifics of an operation. Modernization is a powerful strategy because it is more affordable than building new and allows companies to leverage their existing warehouse assets. Given the wide variety of warehouses and the range of solutions available, it is important to solicit unbiased expertise to evaluate individual needs.
DLN Integrated Systems is a trusted partner that is not committed to using specific brands of equipment or technology. It analyzes each situation uniquely and provides comprehensive integrated solutions using equipment and technologies from a range of manufacturers. This enables DLN to implement the most efficient and cost-effective solutions customized for each client.
The second piece in this two-part series will take the discussion further by relaying a roadmap for warehouse modernization success.