By Marc Gordon, VP of Business Development, DLN Integrated Systems, Inc.
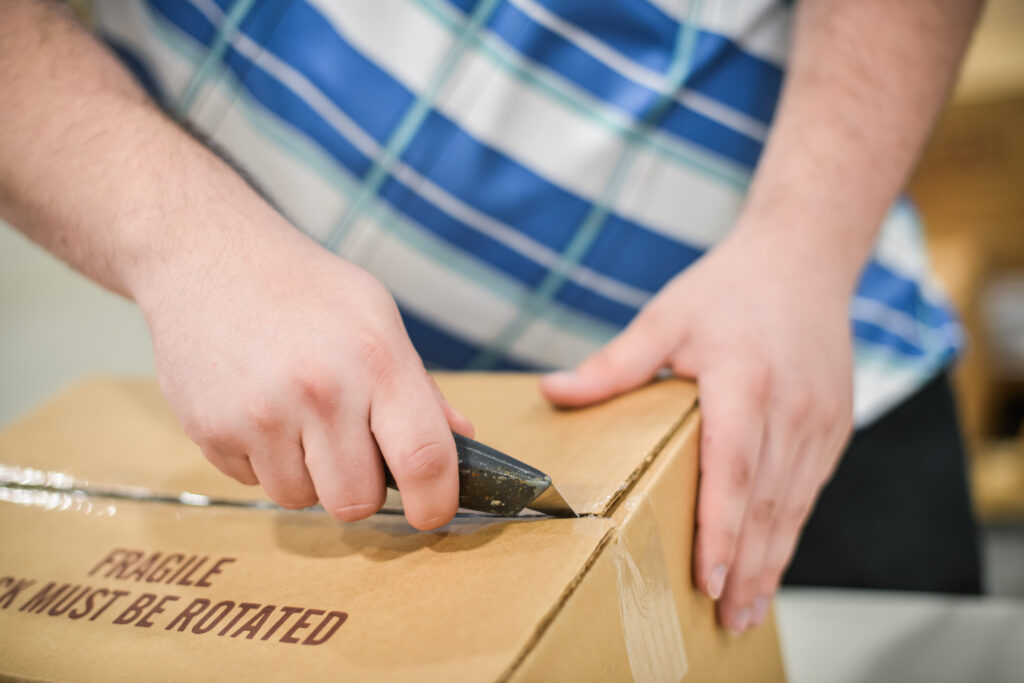
Does that aging warehouse need just a few upgrades or is it time for a complete overhaul?
Legacy facilities present challenges over time as systems age; company needs change; and competitors enhance their capabilities.
It’s tempting to think that the only way to improve your distribution operation is with a brand new, greenfield facility. However, increasingly organizations are looking for less expensive alternatives.
The rising cost of capital expenditures for construction is driving an interest in keeping existing warehouses useful for longer periods of time.
The Importance of Assessing Systems
Organizations hoping to extend the life of warehouses need to assess mechanical, energy, control and other systems.
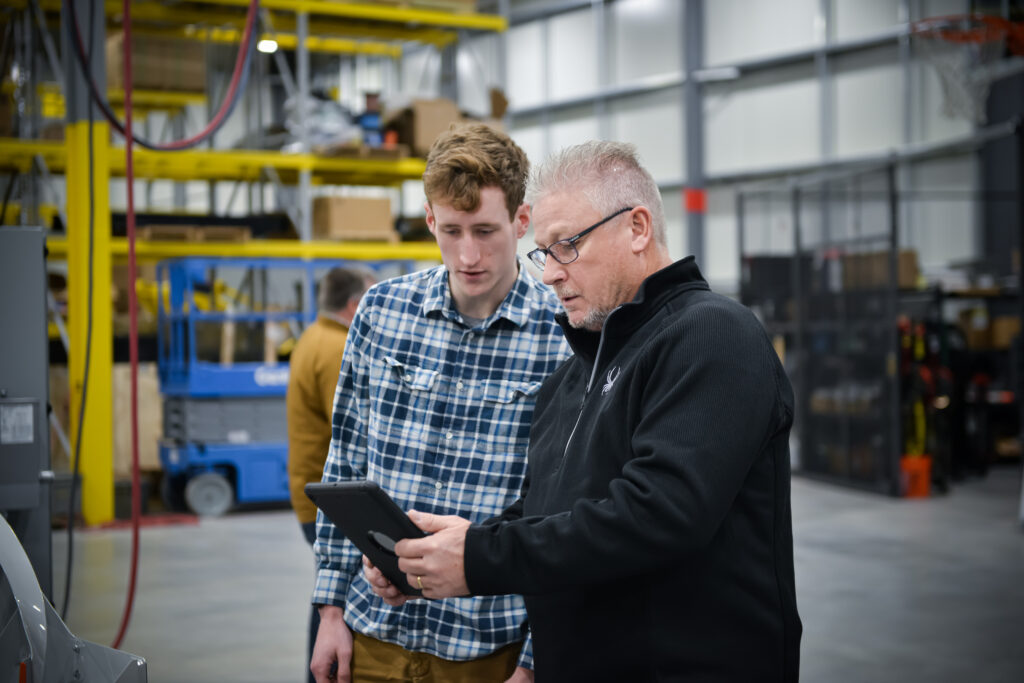
This can drive opportunities for cost-effective, incremental improvements that recapture original performance and, in some cases, even surpass it.
The rapid evolution of technology capabilities in the marketplace typically leaves legacy warehouses behind. Systems assessments can identify the most meaningful and cost-effective opportunities to bring updated technology into older facilities.
Six Critical Steps for Systems Assessment
It’s more important than ever to assess how existing systems can be maintained and optimized to keep legacy facilities robust. Here are some key steps.
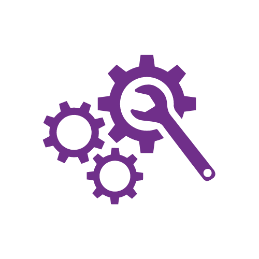
1-Don’t Get Boxed In: Optimize Mechanical Systems
Nothing lasts forever, and that is certainly true of mechanical systems in a warehouse. At some point it’s time to replace mechanical components to enable systems to continue to run as intended. That may sound like a no-brainer, but oftentimes companies don’t maintain and refurbish equipment as they should, which decreases performance and increases both product damage and the risk of failure.
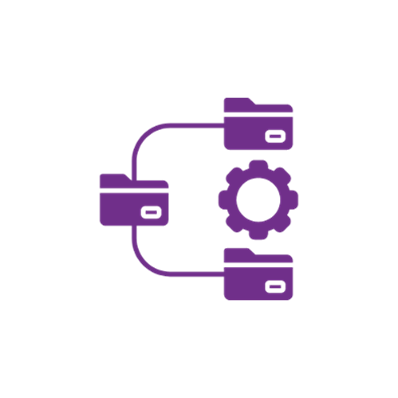
2-Take Control: Enhance Control Systems
Electrical control systems are crucial to operations because they drive equipment functions. It’s important to confirm that older components are still operating as intended and that replacement parts can still be obtained with a reasonable cost and lead time. Beyond this maintenance aspect is a powerful opportunity to upgrade components to make systems run better than ever. This could involve upgrading mechanical sensors to electric photo eyes for improved operational reliability and flexibility. Or it may involve switching out a legacy scan tunnel for a new version with better accuracy and throughput — and even incorporating the ability to record carton images for later use. In these cases, the result isn’t just good as new — it’s better than new.
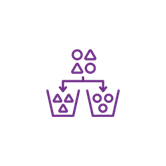
3-Sort it Out: Examine Sortation Systems
Sortation systems perform many critical functions in warehouses, and DCs need to ensure they are operating at peak performance. While all parts of the sorter need to be performing well, many challenges are rooted in problems further upstream — and should be diagnosed by examining the entire sortation process. As one example, if a sorter isn’t tracking or diverting cartons properly, the cause may be an upstream problem with the conveyor feeding it.
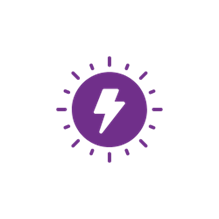
4-Get Energized: Focus on Energy Management
Rising energy costs and tightening of emissions standards have increased the need to focus on energy management in warehouses. Companies can make improvements by tapping into the latest capabilities in the marketplace. One energy-saving opportunity is to switch to run-on-demand conveyor systems and even to obtain functionality that allows for changes in speed. Another opportunity is to move from pneumatic to electrical controls components to reduce operational costs.
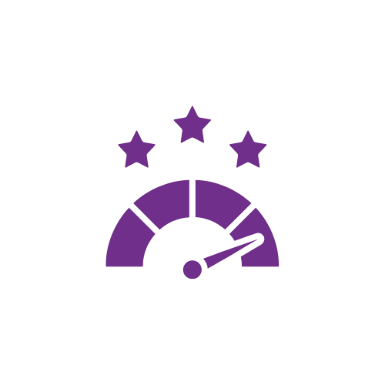
5-Adapt for New Requirements: Boost Performance
Keeping up with growth needs and the evolving competitive landscape may require bigger changes. A warehouse designed 20 years ago for 1,200 SKUs may now be handling 10,000 SKUs — and encountering hurdles along the way. A careful assessment can identify legacy systems that are struggling to meet today’s requirements and point to solutions for progress. In some cases, minor tweaks can be made. In others, an assessment may be the start of identifying and evaluating bigger changes and new sub-systems.
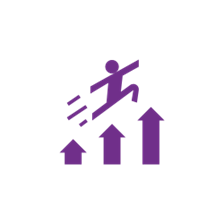
6-Plan for the Future: Consider New Paths
At some point it may become clear that a larger upgrade to legacy operations is needed, which could include a full modernization or even the building of a new warehouse. System assessments and audits can help reach this decision. The key signs include declining overall performance; reduced speed and accuracy; challenges in handling growing assortments or maintaining low costs; and the need for more powerful capabilities to counter competitive challenges.
Gaining Insights Through a Systems Audit
A comprehensive systems audit can assess how a warehouse is faring in all the critical measures. Warehouse operators should engage a partner that specializes in these audits and brings a holistic view in electrical, mechanical and software systems as well as operational expertise for a deep-dive benchmarking analysis. This process typically incorporates a gap analysis to help identify needs and appropriate solutions.
The Dangers of Not Acting
There are major risks in not assessing systems.
One big risk is that older systems might fail and may no longer be supported by manufacturers.
Companies might assume they can get more life out of a system, but they are gambling in making that assumption without a careful review. While it may be possible to ‘muscle through’ inefficiencies of aging infrastructure with increased labor, failing to make critical upgrades and replacements increases the risk of a major failure that could shut the DC down and pose a threat to the overall business.
Drive Success with a Trusted Partner
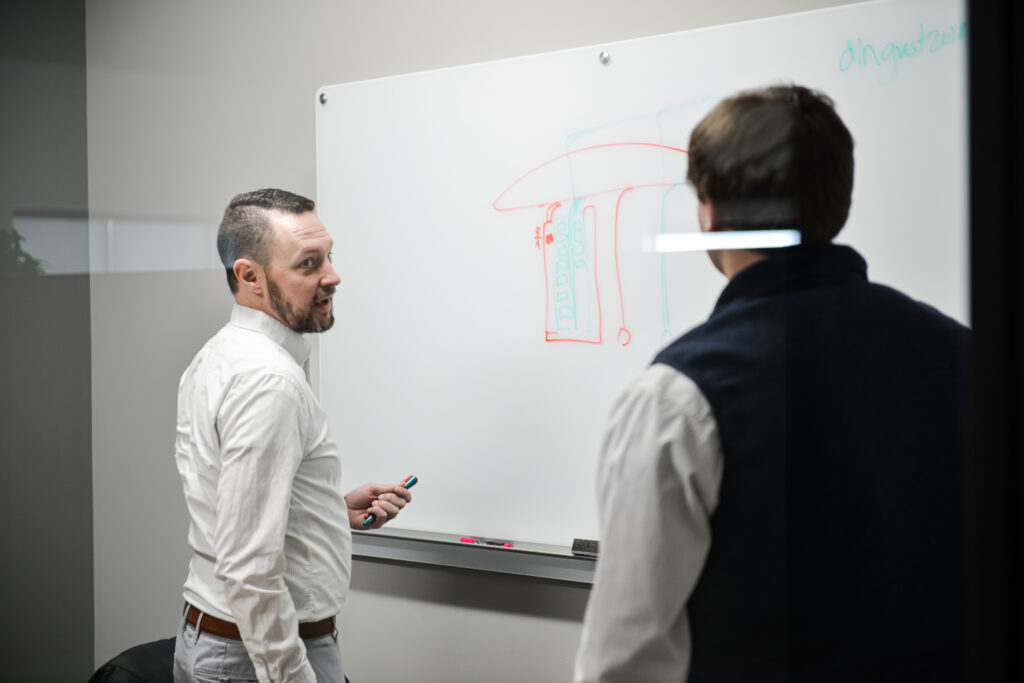
Assessing systems and conducting audits are crucial strategies for warehouse operators. Assessments often lead to ‘quick-win’ solutions that can help get more time out of an older facility at a low cost or may identify an unknown critical threat to business continuity. Working with a trusted partner in assessing systems increases the chances of success. Given the wide variety of solutions in use in legacy operations and the complexity that can come with upgrading obsolete equipment, it is important to work with partners that are highly experienced with modernization projects.
DLN Integrated Systems has extensive experience with modernization projects involving a wide range of operational processes, brands of equipment and technologies. It analyzes each situation uniquely and provides comprehensive integrated solutions with a practical approach to implementation in working facilities. This enables DLN to implement the most efficient and cost-effective solutions customized for each client.