A case for layered process audits in warehousing and how senior leadership can help
We have our metrics. The metrics are posted for all to see and we are constantly talking about the results. If the results aren’t good, we schedule meetings. In order to get the message out, we have more meetings…
The supervisor’s job in this situation is daunting, and they are on the front line. They are teaching people a complicated process. To most people, their supervisor is the company. When your message is in line with the training, it reinforces the mission. The supervisor can use all the help that you can give them!
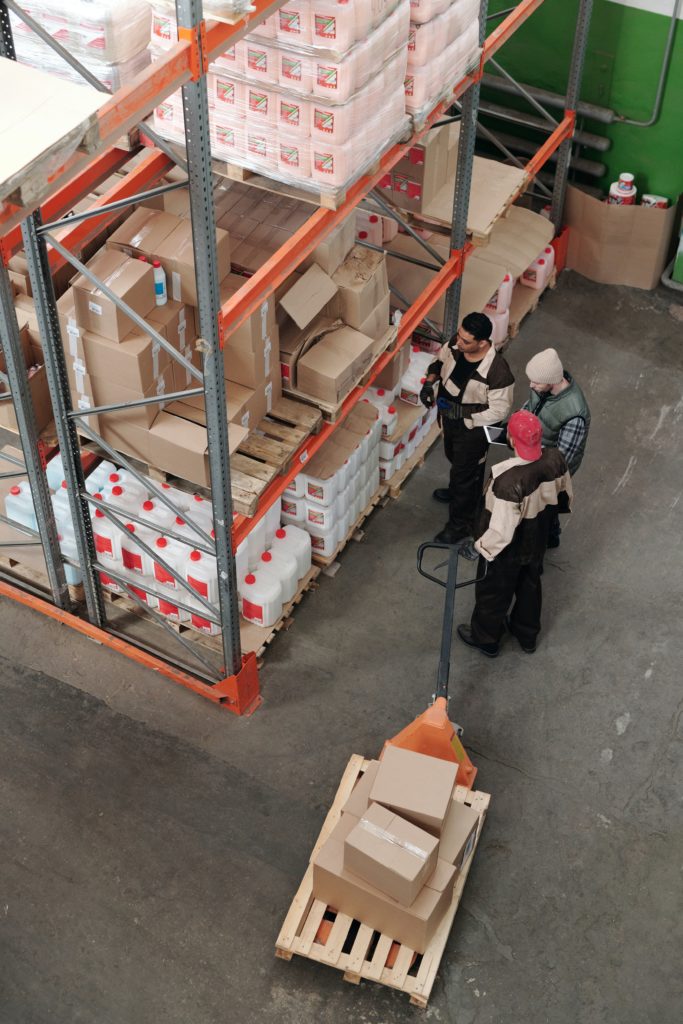
What if I told you that there was a simple task that a senior leader can do to support your supervisor and improve the success of the team?
At specific points along the process, we can observe progress and assess quality by doing a layered process audit. The audit contains criteria that specifically checks for quality components that are essential to a that part of the operation. The results we get are a reflection of saying what we do, doing what we say, and checking what has been done.
Example:
- Good product
- On a good pallet
- Proper label placement
- Stacked well
- In stop order
- Wrapped to ride
“The results we get are a reflection of saying what we do, doing what we say, and checking what has been done.“
This message is meant for managers at all levels. You want to be visible while meeting people and building relationships. It is vital to encourage people to stay with a difficult job until their skills have developed. When you recognize the importance of their work, you’re reinforcing the importance of them.