Part 4 of 5
The first three installments of our five-part blog series A Roadmap to Successful Transformation – can be found here:
Part 2 – Detailed Design & Program Planning (Pre-Implementation)
DLN and Connors Group outlined best practices for concepting and developing the design, preparing the program team and broader organization for the changes ahead, and then managing the actual implementation of the change.
However, true success comes from more than just implementing technology—it’s about using automation to enhance workflows and maintain a people-focused strategy.
While automation helps alleviate the strain caused by labor shortages, it doesn’t eliminate the need for a skilled workforce. In fact, workers are still crucial for overseeing systems, managing processes, and ensuring operations run smoothly.
Whether updating current operations or designing new facilities, a thoughtful, people-first approach is key – with a solid foundation of labor management.
Phase 4 is preparing for transformation with a people-centric approach. But calling it the 4th phase is really a misnomer, as it should be executed in a parallel path to implementation activities, and should be completed prior to go-live to ensure a workforce and management staff that is ready to go live.
Phase 4 – Prepare Your Team
Training and Change Management: Keys to Successful Automation
Adjusting Skill Sets and Roles
Automation often leads to a shift in required skill sets. New roles may emerge, and existing ones may need to adapt. Businesses should assess their teams’ current capabilities and identify skill gaps. Targeted training and upskilling are essential to prepare employees for these evolving roles, such as automation maintenance, data analysis, and system optimization.
Pro Tip:
Develop Thoughtful Training
Consider interactive training modules and hands-on workshops to engage employees.
Building your team’s confidence in the new systems pays off when things are fully deployed.
Change Management for a Smooth Transition
Training alone isn’t enough—change management plays a crucial role in the successful implementation of automation. Both leadership and frontline workers must be on board to ensure a smooth transition. A structured approach to change management that includes clear standard operating procedures (SOPs), user training, and ongoing communication will help mitigate resistance and ensure buy-in across the organization.
Preparing for potential post-implementation challenges is key to long-term success. Automation often requires continuous improvement, so companies should focus on coaching, monitoring, and adjusting workflows as needed to maintain efficiency and productivity.
Operating Efficiently with Automation
Continuous Monitoring and Workflow Optimization
After go-live, maintaining focus on visibility and optimization is key. Use real-time data analytics to gain insights into performance metrics, highlighting opportunities for process improvements and addressing challenges promptly.
Transparency and regular feedback further refine workflows, reducing downtime and enhancing human and automation productivity.
Pro Tip:
Track Performance
Implement a dashboard for real-time performance tracking, making it accessible to all relevant stakeholders for quick decision-making.
Ensuring Seamless Operation Flow
After automation is implemented, ensuring a smooth operation flow becomes part of the regular operational routine.
Regularly review and refine workflows to ensure that all technologies are integrated effectively, preventing bottlenecks and inefficiencies.
Continuously optimizing these processes helps sustain operations that are both efficient and flexible, adhering to lean principles to eliminate waste and enhance quality.
Pro Tip:
Ongoing Process Reviews
Integrate ongoing process reviews into your standard operating procedures.
By engaging cross-functional teams regularly to ensure workflows remain optimized, your team can be responsive to changing needs and can stay ahead of potential issues.
Leveraging Labor Programs for Performance and ROI
Setting Baseline and Targeted Performance
To measure the success of automation, it’s essential to establish a baseline performance metric before implementation.
This allows you to set targeted performance goals that align with your overall business objectives. These goals should be realistic, measurable, and clearly defined to track the impact of automation effectively.
Tracking and Ensuring ROI
Continuous performance tracking is key to realizing the full benefits of automation. Labor programs should be designed to monitor performance against established goals.
Using real-time data, businesses can identify areas for improvement and make necessary adjustments. A well-structured labor management system will help sustain the desired return on investment (ROI) over the long term.
Pro Tip:
Invest in Analytics
Consider investing in advanced analytics tools that offer real-time insights and predictive analysis.
This investment will help you stay ahead of potential issues and optimize performance continuously.
Final Thoughts
Preparing for automation in a newly designed facility requires thoughtful planning and attention to detail.
Automation should enhance the capabilities of your workforce, not replace them. By focusing on efficient operations, optimizing processes before automation, training your team, and leveraging labor programs for performance tracking, businesses can set the stage for a smooth and successful implementation.
Addressing these foundational elements ensures that the investment in automation delivers sustainable improvements and meets performance goals.
About the Authors
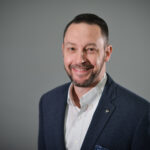
Luke Nuber
DLN Integrated Systems
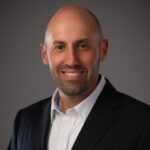
Andy Hunter
Connors Group