Part 3 of 5
In the first two installments of our five-part blog series A Roadmap to Successful Transformation – which can be found here:
Part 2 – Detailed Design & Program Planning (Pre-Implementation)
DLN and Connors Group outlined best practices for concepting and developing the design and then preparing the program team and broader organization for the changes ahead.
With the foundation for a successful transformation firmly in place, it is time to shift our attention to Implementation.
Phase 3 is the Implementation phase of the project. This is where the rubber meets the road and physical changes are made to facilities and processes. The Implementation phase covers a wide range of activities from engineering through the Go-Live of the system.
This phase is clearly mission-critical, as over 90% of the costs of the project will be incurred during Implementation, and future operations will depend on the processes, systems and equipment implemented here for long-term success.
Phase 3 – Implementation
Step 1 – Final Engineering
The first step of the Implementation phase is typically called Final Engineering or Detailed Engineering. This differs from the Detailed Design described in our previous post, in that project teams become less broadly integrated and new teams are formed within each company that are focused on the deliverables of that company to the project.
The functional specifications and drawings produced in Detailed Design are still general in nature. While they cover a wide range of operating conditions, they mostly focus on how the various subsystems interact with each other and the operators to meet the business requirements.
Final Engineering of each subsystem takes the functional requirements specific to that subsystem and adds an extensive layer of detail that is needed to specify, procure and install the equipment and/or software of the subsystem.
While engineering teams will still be interacting with external teams to review details and solve problems, most of the work is done within the individual providers at this stage.
In Implementation phase, all activities and objectives need to be focused on the singular goal of ensuring we are fully prepared for the Go-Live. This includes vigorous management and execution of the program schedule. As discussed in our previous post, the program schedule includes not only the direct construction and commissioning activities of physical and software systems, but also parallel change management workstreams to ensure that people and processes are ready for Go-Live.
Any outstanding issues that impact Go-Live will need to be addressed and resolved promptly to avoid delays.
A Go / No-Go checklist will need to be developed to identify the mission-critical capabilities that need to be complete before the Go-Live is given the green light to proceed.
Step 2: Equipment Procurement & Installation
Although it is the longest (and most expensive) part of Implementation, we’ll skip over the procurement and installation of equipment and systems here.
Virtually any company you will choose to partner with will be able to execute the most basic deliverables of delivering their contracted scope of work.
Unfortunately, there are many transformational projects where each of individual subsystems perfectly meet their stated requirements and yet, the overall system struggles mightily to deliver on expectations.
The difference between challenging and successful transformational projects lies outside of basic implementation activities, so our blog will focus on what makes that difference.
In our previous posts we outlined best practices for developing a comprehensive test plan and discussed how to get your organization trained and prepared to the operate the new system.
With this groundwork in place, it is time to execute the tests and get the system ready for Go-Live.
Step 3: Testing
Start with Subsystem Testing, ensuring that the basic functionality of each subsystem is in place before beginning other testing phases.
Rate Testing is next and is still somewhat siloed by subsystem, although in many cases multiple subsystems will need to be engaged to see any particular subsystem perform at its maximum design rate.
Integrated Testing is the most critical test. Integrated Testing usually follows Rate Testing, but can be worked on concurrently if necessary since the objective is to confirm that all necessary functionality is working as expected but not typically at maximum rate.
Methodically work through each test within the Integrated Testing plan, making corrections and repeating test phases that experience.
Pro Tip:
Work Through Testing Challenges
- It is not uncommon to encounter issues with the process design during Integrated Testing. Make changes as required, but be sure to repeat any tests that may be impacted by the change. Also be sure to update training materials, SOPs and labor standards that might be impacted by changes occurring during testing.
- Plan ample testing time in your project schedule and start it on time. Rushed or skipped tests leave hidden issues undiscovered and uncorrected heading into the critical Go-Live. Working through problems in a live system is far more expensive than fixing them during commissioning.
As testing concludes and Go-Live approaches, work through the Go / No-Go list of mission critical functionality that needs to be in place and confirmed prior to fully committing to the Go-Live. It is not reasonable or realistic to expect the system to be 100% perfect at Go-Live – even if it could be achieved at the start, mechanical systems always experience a spike of minor failures as the system is run-in and faulty parts are discovered – but if the Go / No-Go list was carefully created it should be fully achieved before the final call to Go-Live is made. Prioritize correcting items on the Go / No-Go list to ensure the system is ready, leaving those issues that don’t significantly impact performance for later.
Pro Tip:
Plan Ahead for Disaster & Recovery
- Despite the best efforts of project teams to prepare for Go-Live, there will always be an element of risk of encountering a disaster scenario, especially for major transformations. Avoid amplifying these scenarios by planning ahead for the worst-case scenarios.
- Brainstorm and document various plausible scenarios that could occur.
- Then work through a recovery plan for each, including work-arounds to continue supporting the business, and train support teams on those recovery plans. While there still will likely be significant pain associated with the disaster, the investment in disaster and recovery planning to minimize the disruption may prove to be a worthwhile investment.
The Implementation phase does not end on the day of Go-Live, as there are a significant number of post-install activities required before the system is ready to transition the ownership from 3rd party Implementation contractors to the in-house operation team.
Step 4: Post-Install Communication & “Hypercare”
The 1-2 months following Go-Live are typically a “Hypercare” period where outside resources from the various consultants, technology providers and integrators that designed and built the system are heavily involved in resolving technical, process and training issues that escaped the test and training plans.
Also during the Hypercare period, the installation teams will be working to resolve ‘punch list’ issues which are various system defects that are not critical enough to stop the system from going live.
Step 5: Post-Mortem Meeting
Lastly, before program resources fully disengage and hand the system over to operations and system support teams, a post-mortem meeting should be conducted.
The post-mortem is a thorough review of the project history and current operations. It is typically conducted approximately two months after Go-Live and is valuable to all parties involved as a way to gain insights on what can be improved in the future.
The system is now live and creating value for the organization! Although it may not feel this way after several years of intensive effort, if your team has carefully followed the best practices outlined in this blog series, you’ve put in the work to minimize your risk and accelerate the learning curve for your team.
But the work does not stop here! Be sure to check out the fourth installment of this blog series to learn more about best practices to keep the system performing at high levels for many years to come.
About the Authors
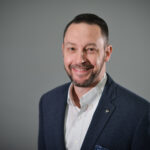
Luke Nuber
DLN Integrated Systems
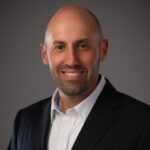
Andy Hunter
Connors Group