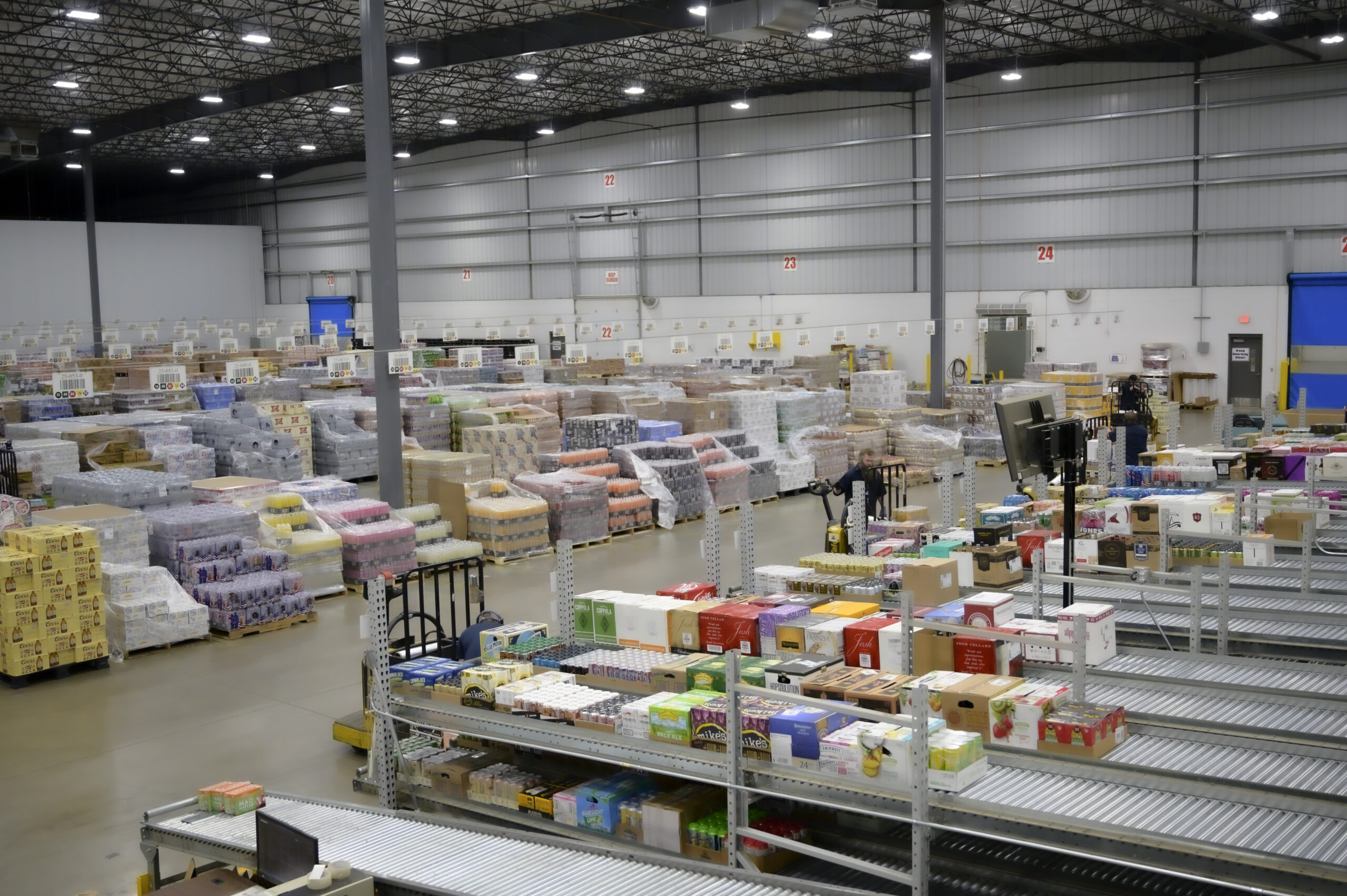
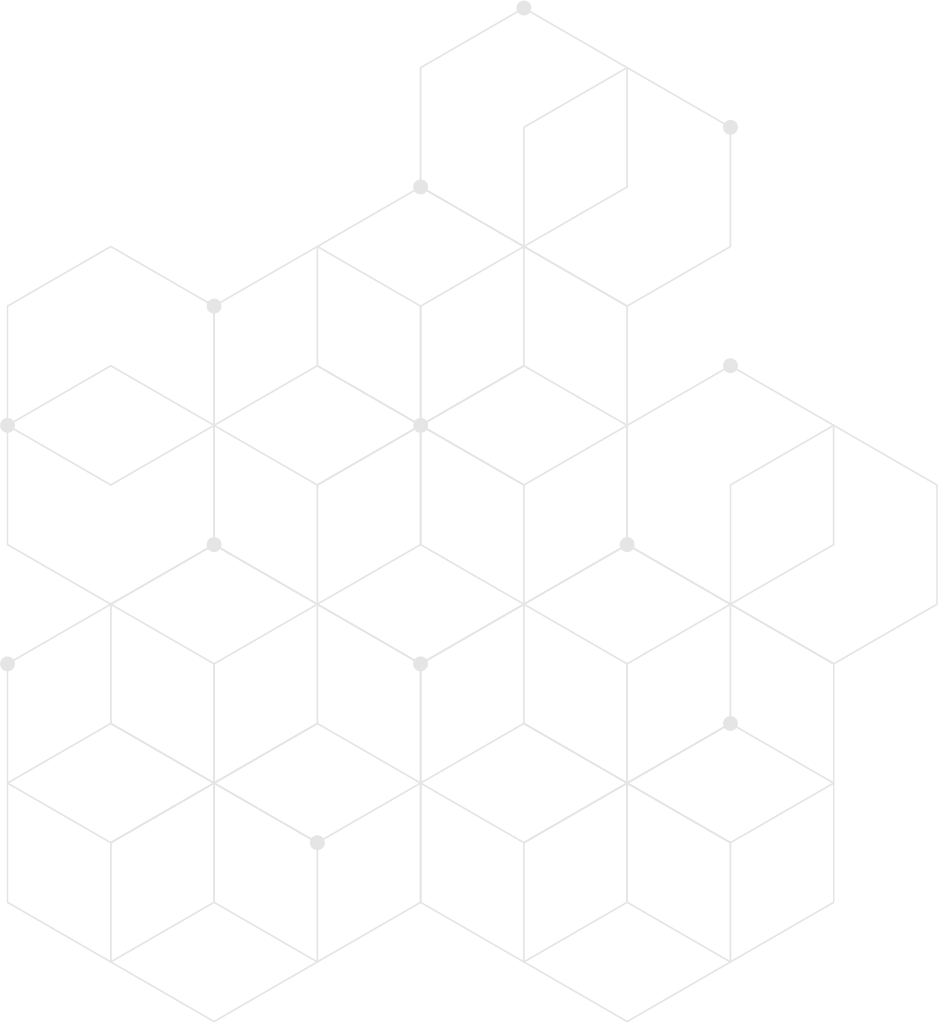
Consolidate Multiple DCs
Client:
Alliance Beverage Distributing
Industry:
Food & Beverage
Solution:
Distribution Systems Integration
Alliance Beverage Distributing was created in 2013 with a merger that required a new distribution center to handle the boost in volume from consolidating 3 separate facilities into one.
Challenge
- Post-merger need to consolidate 3 cross dock DC’s handling 5200 SKU’s into 1 facility
- Process rate was 90 cases per man hour
- Flexibility for seasonal demand surges and future growth, with slow movers handled separately
- Re-use as much existing equipment as possible and maximize floor space, and incorporate automation for labor-intensive tasks
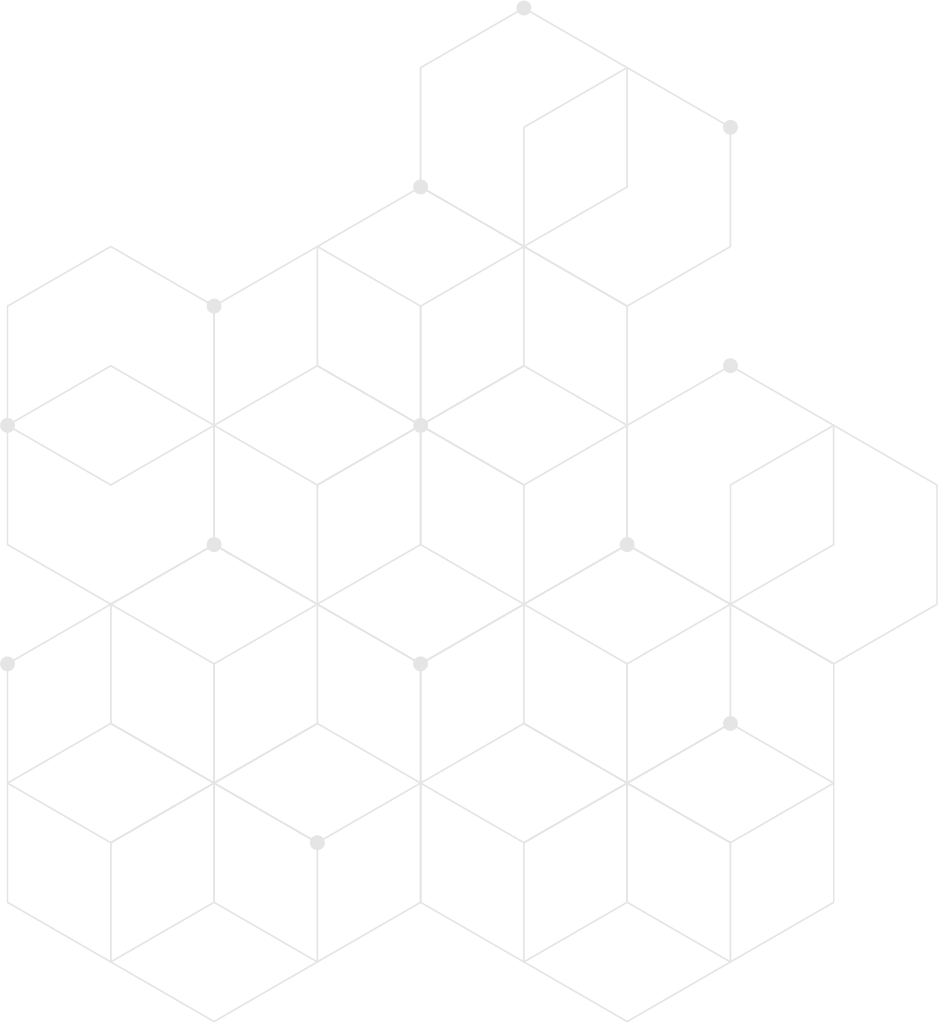
Solution
- DLN designed a 300,000 sq foot DC with efficient picking, sorting and palletizing based on groups of orders
- Automated pallet handling includes quality control with weighing for quality control, then wrapped for shipping
- System could easily flex for expansion and to handle seasonal spikes in demand
- Picking platforms saved on floor space
Results
- Orders processed faster and more accurately
- Picking errors reduced by 85%
- Orders processed at 240 cases per man hour (CPMH)
- Reused 30% of existing equipment
- No interruption to daily operations