Part 2 of 3
This post is part 2 of 3, covering DLN’s educational conference Optimizing Supply Chain for What’s Next, held in May 2025.
See Post 1 of 3 covering consumer trends.
After a break and an intense room-wide game of rock, paper, and scissors, Shattuck introduced everyone to Dr. Dan Pellathy, Faculty of Practice at Haslam College of Business University of Tennessee-Knoxville.
The experienced supply chain scholar, who has been published in many leading academic journals, asked how many people were actively recruiting supply chain talent.
Nearly half the room raised their hands. Then he followed up with how many people were having success and felt they had a good process in place.
No one raised their hand.
Thankfully, Pellathy provided ideas and hope because of a new American Productivity & Quality Center (APQC) report titled Supply Chain Planning Talent Management: Cross-Industry Report.
Developing the Next Generation of Supply Chain Talent
He said because the supply chain can significantly impact the bottom line, many companies are re-examining the skills needed by supply chain planning professionals for future success.
Plus the competition for supply chain talent is fierce and will only grow as leaders lean on the supply chain to manage change, incorporate new technologies, and navigate ambiguity.
Therefore, to determine how organizations are developing and investing in supply chain planning professionals for what is to come, APQC conducted research in late 2024. Pellathy and his team created the report based on 462 valid participants.
A key finding he led with was only about half of company leaders prioritize in-depth training for supply chain planning staff. With all the changes in the industry, they concluded this reality was dangerously short-sighted.
The Needed Skills
Pellathy went on to share that respondents felt supply chain planning professionals will need a blend of deep work, social skills, and technical skills to be successful.
Technical skills, though, are often top of mind for leaders at the expense of the other skills.
“(Technical skills) are not the entire organization,” Pellathy said.
But whether it’s deep work, social skills, or technical skills, they can’t be developed overnight. They require a company to roll out a slow, intentional strategy to employees.
“These are all hard,” Pellathy said.
Next, he shared more specific skills within each of those three important categories.
Pellathy defined deep work as focusing without distraction on a cognitively demanding task. He said the most desired deep work skill was critical thinking, the analysis of facts to determine a course of action. Complex decision making and innovation also were ranked highly.
Yet with all the digital distractions in today’s business world, critical thinking is challenging, he said. That’s why many companies are requiring more off-site meetings without technology to cultivate this skill among supply chain planning professionals.
Top Social Skills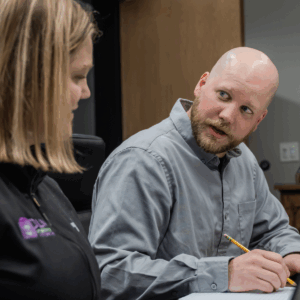
Moving on to the top social skills, Pellathy said these three came in highest:
- Oral/Written Communication
- Stakeholder Management
- Change Leadership
“Supply chain planners need strong oral and written communication skills to understand the needs of the business, clarify expectations with multiple internal stakeholders, and maintain positive relationships with both suppliers and the business,” the report summary stated.
Top Technical Skills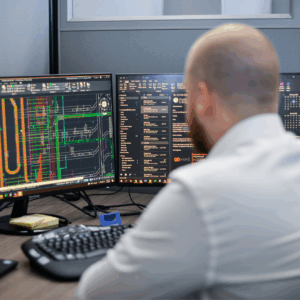
Pellathy said respondents revealed the top technical skills were:
- Demand Planning/Forecasting
- Data-driven Decision Making
- Data Analytics
Demand planning provides accurate prediction of customer demand which leads to optimized inventory levels and efficient operations.
Furthermore, understanding the context of the supply chain data, not just the analytics, is very important, Pellathy said. That’s why he’s seeing a trend of companies requesting graduates with a supply chain major and an analytics minor.
The Struggle of Training
Pellathy then shifted to highlighting the gap between the importance and effectiveness of deep work skills, social skills, and technical skills.
Overall, many companies were struggling to provide effective training and development for these skills. Even for the skills at the top of the list, he said respondents rate fewer than 40 percent of organizations as very or extremely effective in their talent development.
“Organizations aren’t happy with their developmental programs,” Pellathy said. “…Organizations should invest more in helping supply chain professionals close these critical skills gaps.”
He said deep skills and social skills are more challenging skills to teach and develop because they require more tacit (vs. explicit) knowledge and expertise. As a result, he reiterated once again that companies must be more intentional.
The Role of AI
Despite a growing interest in AI, Pellathy said only about one-third of organizations report active AI use in supply chain planning (i.e., implementing, operating, or optimizing). A significant majority remain in the piloting, consideration, or evaluation stages.
Most respondents said increased AI usage will require the development of technical skills in data science, machine learning, and modelling, analytical skills with business acumen, and strategic thinking.
Opportunity: Transferring Knowledge
Pellathy finished his presentation sharing that out of 19 talent-related goals, organizations report the highest effectiveness in providing employees time to learn (35%), with the lowest effectiveness in knowledge transfer (16%).
This is telling: while companies recognize the need to improve the skills of their employees, they lack robust systems to capture and share expertise—especially as seasoned employees leave.
Click for Part 1
Covering consumer trends through the lens of supply chain!
Click for Part 3
Covering modernizing your facility for competitive advantage!